Navigation Menu

RG500 Cylinders part 1
Well Well Well. This is a popular one, eh?
What can you do with the RG's cylinders? Or.. what CAN'T you do with the RG's cylinders?
Think of this as not having a single, fixed answer. You can do a lot of things with a single-exhaust, iron-liner 2-stroke.
You can make it a steady, reliable, slow street bike (Think Titan 500).
You can make it a faster street bike. (Think OEM hi-po streetbikes)
You can make it really fast, with a far greater risk of failure. (Think every souped-up RD350, H2, RG etc that has tales of speed mixed with destroyed components. )
Part of this has to do with our ability - or inability- to control all the variables as we step ever closer "to the edge". Some of those blow-ups are just plain gonna happen if you have a ton of advance and 84 octane gasoline.
So how far can you push it? Well... how long does it need to keep running?
You can make a LOT of power for 10 seconds. If you parts can absorb the heat for 10 seconds without failing, you can build a nice drag engine. Maybe you run an exhaust port so wide the rings are only good for 50 miles, but that's a long time in this application. Maybe it runs so hot that you're just starting to hit an excessive amount of detonation in 9 seconds. Maybe the piston is starting to overheat after 10 seconds, and the rings can't shed heat into those poorly-conducting iron liners fast enough to go any longer.
So yeah - for 10 seconds, you can get away with a lot.
Or, maybe you're Shane Kennealy, running an RG at Bonneville. His engine runs WOT for three miles. The timing traps are two miles long. That's somewhere around 50 seconds at full power, top speed, full throttle. That's a very different thing than holding together for 10 seconds!! His engine has to deal with peak heat and loads for an eternity, relatively speaking. He simply can NOT work with the same parameters as the 10-second engine. Fortunately, he has a 150 mph wind blast through the cooling system! He can run a super-rich oil ratio, if he wants -- as long as it fires, the more the better. At WOT plugs tend to stay pretty clean if you've got the ignition to fire it.
Maybe you're a road racer. Your engine has to run well at all throttle settings, it has to pull up and down thru the range- you may be on a short track, with not so much airflow at lower speeds. You run down a straightaway, only to slam on the brakes and slow to a crawl for a hairpin, while heat dumps into the cooling system, raising temperatures. You may spend seconds upon seconds at high rpm and light throttle in a long sweeper. Maybe you can't just run that super-rich, oil-heavy premix ratio and keep your plugs clean. In short, your engine may have to live 20-40+ minutes under racing loads and conditions. And, you want it to do this reliably. Again, a different set of rules are in play.
I have done trackdays and road racing with my bike, ever since I started tuning it. So in my case, I operate under that third set of rules. Even so, I have always been leery of wide-open tracks with long straights. I used to do a lot of experimenting on the street, trying to find out how fast my bike could go (about 135 when I first got it) and I have blown it up more than a few times on the street and on the racetrack. Yes, I have seized it hard at the top of 6th gear. That's quite exciting! It's amazing that one piston can stop the whole motor in an instant, but I'm here to tell you, it sure can. At least the clutch still works, which is more than I can say when the transmission breaks!
I'm clinically lazy, and cheap, and dislike taking my engine apart constantly- even though that seems to happen anyhow. But I don't want to say- "Yes. This engine will have a service interval of 250 miles".
So, as I see it, what holds the RG cylinders back from making 160 hp?
Well, I just don't think it'll survive under racing conditions at that level. Not for long. If you had a look at the 100 HP page, you'd now be up to speed on BMEP. Think of it in turbocharging terms, maybe. A low BMEP engine is like a turbo engine running on 2psi of boost. No big deal. Yeah, you can raise compression and tune for very high BMEP, but now that's a 10 psi engine. Those are more dangerous waters. The iron liner is a poor heat conductor, which is too bad because the piston dumps its heat into the liner... and at some point, with that iron liner slowing the process, it means the piston can't get rid of heat fast enough to keep from going over-temperature.
That's why every newer-generation 2T has an aluminum cylinder and liner.
That's why water-cooled bikes can make more power, for longer, than aircooled bikes. You get the picture. The RG's barrels are an older technology (Single-exhaust, with steel aka "iron" liner cylinders) and have some limitations.
But, working with what you have - you can still go pretty crazy.
Think back to what this generation of GP bikes were able to make for power - you can't lay it all at the feet of the cylinders, but they did push things to the limit of reliability. The 1981 RG500 'Gamma" as labeled by the factory, was rated at 130 hp. I would assume this was still an iron-liner bike. It could make that level of power for race distance, or run at the Isle of Man - granted, on racing fuel, but the thermal limits of the cylinder and pistons were probably similar to ours - or worse, since piston materials have gotten better. Hmm.
Well, at the 126 hp level, I suffered several broken pistons (ring lands breaking), seemingly a byproduct of detonation, however sometimes with no visible signs of deto. Before we get into deto, let's just say that a hot piston can certainly be a factor. Was I running into a limit in this area? No idea. I did not put in the required effort to dance right along the edge of reliability, and I used pump gas, my personal nemesis. But after those broken parts, I started to look for a better parts to fit into the engine. More on that later. I think as a casual street engine, I could have easily stayed with the OE cylinders. A burst of speed here and there is not a problem. Plenty of guys have got big HP from the OE barrels, although almost all seem to have 550-570 cc engines. But, plenty of guys have melted down big CC, big-power motors on trackdays.
If I were a betting man, I'd say that building an iron-liner RG past 135 HP and taking it racing is sketchy - and going to require very specific attention on your part to MAKE SURE everything is working right. You have to be "that guy" , checking plugs frequently, jetting for morning weather, using cool-burning, high octane race fuel, running an adjustable ignition and keeping it just this side of trouble, and running as much oil ratio as you can bear. Reading Suzuki's racing history on the XR14 and earlier bikes, they used very rich oil ratios at times and plug fouling was common, Martyn Ogborne mentioned oil ratios of 20:1 (!!!) on the XR14.
Porting:
How to understand what'a going on in here? If you're new to analyzing a 2-stroke, there are some great reading resources for you. I'd send you over to the tech playground portion of the website for more info and links, but always worth mentioning are:
A. Graham Bell's 'Performance Tuning"
and
Gordon Jennings' "2 Stroke Tuner's handbook"
These are not brand new, but they are full of sound information. So if you have to start somewhere, start there!
Here's a great little article by Eric Gorr on analyzing an engine's porting and specs - this used to be posted on the TSR website (now defunct). Most of these programs (or close to it) can be found in the Tech Playground section of the RG500 resource.
The transfers IIRC are pretty well-set at the stock heights, to support a peak at 10200- 10500 RPM. You don't have to worry about raising the transfers on the RG's barrels. I did try that, once by actually porting them, and once by using a cylinder base spacer to raise the ports. The eventual 126 HP engine had transfer ports reduced back to the stock heights. With epoxy. They can be quite ugly, though, and should be cleaned up and matched from liner to casting.
What about the bottom of the transfer ports, which are not uncovered by the piston? Isn't that lost potential? This was a great response to such a question:
"Q: >Maybe just modifying the piston crown at the rear port (to fully open the tansfers) will provide that extra "oomf" that we're looking for. Who knows!<
A: "Don't do that! Remember, IF it's the "incomplete opening" of
the transfers that you are referring to (in other words, the piston's "port
timing edge" doesn't uncover the entire port "opening"), this is entirely
normal and in nearly all cases doesn't hurt port flow at all. True, a
perfectly looped transfer passage that "funnels" ever smaller until it
enters the cylinder and matches the port floor at BDC is the absolute
optimum, but the "upper roof" shape is FAR MORE IMPORTANT than the floor!
Don't concern yourself too much with this "floor", it will
make little difference because the GREAT MAJORITY of the flow is at the
roof anyway - AND, the bulk of the crankcase charge (guesstimated at around 70 to 85%) is completed before the piston EVER gets to BDC anyway (another guesstimate at around 50% port "open area" = greatest flow) - so you never have a perfectly formed "floor" before nearly ALL the case flow has occured no matter what you do!"
The exhaust, however, is a different story. It's definitely on the conservative side, as far as width and opening timing. I have seen a number of cylinders where the exhaust opening in the liner is poorly matched to the casting, as well. It helps to blueprint this stuff.
Port shape
The RG has a single exhaust port, as opposed to more modern cylinders which have either a larger, bridged port (ring support in the middle) , or a triple exhaust (a large main port flanked by two smaller sub-exhaust ports).
The single port pplaces a limit on the amount of exhaust area (and thus, "time-area") available to us. This is not really an obstacle to making 125 hp, but a triple port with a set amount of time-area is simply going to be much easier on the rings than a giant, wide single port. So again, newer stuff is simply a better design.
We could say , "But WHY didn't they do this or that?" Well, the RG only made 90+ hp out of the box. There was another 30 hp of potential in there, with the barrels that came on it. So, Suzuki didn't exactly give us the shaft on that one.
Exhaust Timing
Since it opens a little on the late side, you'd think, "This is a good thing for low end power!" And in some ways, it is. However in our case, the low exhaust in conjunction with high-ish transfers leave us a little short on blowdown time-area. (blowdown is a way to quantify time for the cylinder pressure to drop before the transfers open. If the transfers open when cylinder pressure is greater than the pressure in the case... spent gas from the cylinder will push down into the transfer ducts.) Plus, the exhaust timing and transfer timing really aren't in synch with each other. The RG is really begging for the exhausts to be raised.
When Eric Gorr did my cylinders, he pointed this out to me, and said that raising the exhaust port would increase blowdown , and, surprisingly, would help my mid+upper mid power in addition to top end because of this improved parameter. Raising the exhaust wasn't just a "add 500 RPM on top" thing.
Port width
So, if you're the porting sort, the rule of thumb is keep the exhaust under 70% of bore width- measured straight across the port opening. 70% of a 56mm bore is a bit over 39mm. 74% is around 41mm, and that's really about as far as you want to push it if you want things to last a long time. And by 74% you better know what you're up to as far as properly chamfering the port to treat the ring gently. So with the exhaust somewhere in that range, and raised to the right extent, you can get an RG to peak very strongly around 10500 RPM. Trying to force an RG to peak at 11500 or 12000 by putting a really short pipe on it is kinda of futile. The ports overall are really in good shape for 10500, though, once you work on the exhaust.
Here's a note from James Hunt, a tuner I was working with, back in the OE barrel days:
>>Randy, I looked at the port timing and for a 10500 to 11000 rpm peak I come up with something like -
Ex: opens 81.78 degrees or 24.88mm atdc <<
I would also add this. Unless you're going to optimize everything you can inside the engine for more power, pushing it to the limit on the exhaust port width is the wrong place to cut into your reliability. You know, you have a 105 hp engine... don't go for 75% chord width on your exhaust. If you really want 2 more Hp, look for some lower-hanging fruit!
More on maximum port width:
Typical chord= 70 percent of bore width
57mm bore = 40mm chord
Radius port entries 1.5mm radius
some race sleds up to 78 percent
And this, regarding RZ350 porting:
"I have a set of cylinders ported by Gary at
Spec 2, and as per our many discussions
on the subject, he cuts his exhaust ports
43mm across (67-68%) on stg 3 tune."
Here's a great article from Wiseco on excessive port width and the effect if has on other things! A bit of a surprise!
http://blog.wiseco.com/2-stroke-locating-pin
And finally, a comment from a Canadian madman who pushed the exhaust port to the absolute limit, in a racing application:
"The little rg4 is a blast but unreliable. My fault, I leaned on the motor HARD. The exhaust ports are a sneeze too wide at the top. As cranks turn backwards F cyls are fine, the R have the rods trying to drive the piston out exhaust so the rings snag at the top. The R rings are broken after 2 race weekends. But it wreaks havoc even in bigger classes. Here is mosport, top of 4. Finished 8th from 36 gridded...........in the 600SS class!!!"
More transfer port terminology and discussion
by Rustie
"So all of us know exactly how the ports are named, allowing us to
communicate better about them, they are (proceeding from the exhaust port around towards the rear:
First pair = MAIN TRANSFERS (or MAIN's);
Second pair = CENTER AUXILIARY TRANSFERS (or CENTER AUX's),
if NO third pair, drop the word "CENTER";
Third pair = REAR AUXILIARY (or REAR AUX's);
Final single or paired "rear port/s" = BOOST PORTS (or just BOOST).
Lately, we've been seeing the manufacturers use larger AUX's than MAIN's, with a solid 90 degree roof angle (for more midrange punch) aimed directly towards the center of the piston. This doesn't seen to "short circuit" and blow case charge out the exhaust as it would seem because the MAIN's oppose this flow.
It appears that the optimum is to have the MAIN's and all AUX's stagnate their charge energy in the center of the piston crown causing a column of fresh charge to rise towards the head, not unlike a "non spinning" tornado, with verrry good stratification. For this "cancellation of port flow energies" to occur, the accuracy of the upper port opening edges in the liner are FAR MORE IMPORTANT than any floor levels.
In addition, we've seen "staggered" MAIN's (1st to open), AUX's (2nd to open - w/no REAR AUX's) and BOOST (last) by as much as 1.5mm's each in a 72mm stroke (don't remember the degrees). This promotes "charge tumbling" for even more stratification (I wouldn't stagger the RG ports by any more than .5mm initially). The boost have been aimed many different places, like towards the spark plug to just above the exhaust port to a complete 90 degree like the MAIN's and AUX's, aimed at the center of the piston, towards the exhaust.
Older technology had the MAIN's the largest and aimed just about where they are today or maybe @ 75 degrees, with the AUX's aimed towards the rear of the cylinder and sometimes at an even higher 60 degrees or so. Boost, until lately have nearly always been aimed very high, sometimes as much as 20 or even 15 degrees. Times have changed!"
Transfer duct outlet shape:
email on duct exit shape- rounded or not
Or to put it simply:
Top of ports need be sharp as possible, soft stone chamfer into window.
BIG BORE
OK, so a lot of RGs very successfully run big-bore engines. My 516cc OE-barreled engine had a terrific power spread and I've ridden some really fantastic big-bore RGs. I think it's a great way to improve this engine, especially a street engine. Or, as a track engine if you build it with a set power level in mind. Elsewhere, we'll talk about the inlet port, and what I think is its restriction on ultimate power potential in the RG engine. However, a big bore gives us some leverage to use against that intake port.
Big engines suck HARD on the intake port, and you can get some great intake velocity with a smallish port... leading to nice behavior, as far as carburetion! In the car world, sometimes you can get better power when using a restrictive head, by using a shorter connecting rod. The short rod = higher piston speeds = more suction on those little ports.
Here's an interesting exploration on the advantages of just adding displacement! Not on an RG, but same principles apply. For example, what will happen when you add 10% displacement and use the unchanged ports? Courtesy of Vincent Crabtree.
Here's Vincent going through an analysis on an RZ350 engine - a great exercise in learning how to apply these techniques:
One thought here is that the piston crown absorbs a lot of heat. It then has to pass that heat to its edges, through the ring, and into the cylinder wall. I guess you do get some nice cool charge to help absorb heat, as well (an unwanted situation) .
I have used this analogy one too many times, but I'll drag it out again here. The piston crown is like a fuse in your fusebox. Iinsted of electricity, it carries heat. A small, thin fuse will blow uder high current flow.
A thin piston crown can overheat when faced with more heat than it can transfer. A hot crown can sag like warm taffy, or easily have a hole punched through it.
A thick crown can pass far more heat, and can also absorb much more heat, just like a 50A fuse can handle more current than a 20A fuse.
Where do you usually poke a hole thru a piston? Generally, in the middle.
So if you put bigger and bigger pistons in the engine, that heat has to travel a loooong way out to the edges. Make sure the piston crown is up to the job. A racer friend told me that Rich Oliver could run more compression and ignition advance in his TZ than the other brands could- in part because of the fat, heavy piston crowns of the TZ, with their generous heat path.
I have a suspicion that smaller-bore pistons prove to be more robust than big-bore pistons in an RG, when you push them thermal extremes. Now, since we have put holes in plenty of OEM 56mm RG pistons, this may not seem like big news. But since running TZ pistons, my engine has (accidentally) endured detonation that would SURELY have holed my old RG pistons. They have been absolute monsters, as far as ability to absorb punishment.
Re-sleeving
Manny U.
"There are two ways to re-sleeve a cast-in sleeve'd cylinder such as the RG. The common way is to use a thin wall sleeve which only strives to replace the portion that has been worn from use. On the Gamma, this sleeve will measure about 60 mm O.D. and leave the primary sleeve intact for support. This works fine as long as there is no structural damage to the body of the original sleeve, i.e. no cracks or broken supports at the base. This will only be useful on 56-57 mm bores, not the 59 mm motors since there's no way the extensions would hold up at the base if they are 0.5 mm thick or less. If one were to break off, the motor would be junk in no time.
The only way to repair a broken sleeve is to bore out the existing one entirely and replace it with a thick wall sleeve with the same maximum O.D. as the stock sleeve supports at the base (66 mm). This would replace the stock sleeve with one that is 66 mm from top to bottom with a retaining lip of 68 mm at the top to lock the sleeve in place between the head and cylinder deck. The thin wall sleeve also must be retained with a 62 mm lip at the top to locate the sleeve.
Sleeves must be installed from the top down so that the retaining lip comes to rest in a machined groove in the cylinder deck and is captured by the head, preventing sleeve shift when in use. Thin wall sleeves require minimal port correction. The thick wall type removes all ports and will be a challenge to reconstruct the proper port shape and angle approaching the bore. These will make for very heavy cylinders as well."
These are not images of an RG cylinder, but it IS a nice visualization of the ports inside a 2T barrel. In this case, likely a single or V-twin with lots of room for wide transfer ducts. Since the RG's barrels are nestled closely together, there is not enough room for wide, gently arched transfer ducts. A modern 125 can make 50+ hp per cylinder, however there is no way such a cylinder could be fitted to an RG. They are simply too wide - and this illustrated where that width comes from.
Base Gaskets - which is which?
RG 500 Rear Cylinder Base Gasket 11242-20A00-H17
RG 500 Front Cylinder Base Gasket 11242-20A03-H17
A03 = FRONT (4 holes)
A00 = REAR (2 holes)
Cylinder anti-wear coating
"The carbide bore process combines the best features of ceramics and cast iron cylinder bores. This evolutionary process of impregnating diamond-hard silicon carbide particles into the cylinder wall is truly a technical advance directed at the problem of bore surface wear."
I had this done on one of my bikes, however I changed to the TZ cylinders and never really had a chance to evaluate long-term wear with the Bore-Tech cylinders.
Powervalve orientation
From Rigas : "The little line inside the PV faces to the piston side.
If placed to the wrong way around this makes the valve's home (open) position not to be full open I think.
Probably this will make it when turned to the high rpm position to be more around so reveals some area instead of full closing the area."
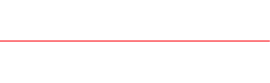
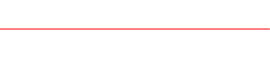
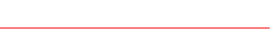


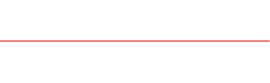

Using epoxy in ports?
This comes highly recommended:
Also: Moroso A/B epoxy for the TZ crowd

